Hochdruckerzeugung
Es gibt unterschiedlichste Technologien, um Hochdruckanwendungen für Werkzeugmaschinen zu erzeugen. In Abhängigkeit auch vom Medium, also hauptsächlich von dessen Beschaffenheit und Viskosität, unterscheidet man zwischen optimalen und nicht leistungsoptimalen Pumpen. Da wir uns im Bereich des Kühlschmierstoffs in der Regel mit zwei Kühlmedien beschäftigen, konzentrieren wir uns auf Pumpentechnologien, die sich in Verbindung mit Schneidölen und auf Wasser basierenden Emulsionen (min. Öl-Anteil von 8 %) bewährt haben. In den letzten Jahren sind auch viele biologische Kühlschmierstoffe, sowie synthetische Kühlschmierstoffe auf den Markt gekommen, die wir mit unseren Pumpentechnologien grundsätzlich bedienen können. Je nach Anforderung und Anwendung, bieten wir vier Lösungsansätze, unterschiedlicher Pumpentechnologien an. Bei der einsatzbezogenen Auswahl, stehtgleichermaßen im Vordergrund, die Effizienz in der Hochdruckerzeugung nachhaltig zu verbessern und die Prozesssicherheit zu steigern.
Art der Pumpe | Bemerkung | Effizienzklasse | Max. Druck bei Öl* | Minimal erforderliche Mediumreinheit |
---|---|---|---|---|
Kolbenpumpe | Leistungsoptimale Pumpe, gerade bei hohen Drücken. Hoher Wirkungsgrad. Verschmutzungsanfällig. Benötigt gute Filtrierung. | 70–95 % | 300 bar | 30 µm |
Zahnradpumpe | Leistungsoptimale Pumpe. Verschleißt schneller bei hohen Drücken und Dauer- einsatz. Hoher Wirkungsgrad. Verschmutzungsanfällig. Benötigt gute Filtrierung. | 70–90 % | 100 bar | 40–60 µm |
Schraubenspindelpumpe | Verschmutzungsunanfällige Pumpe, aber mit relativ schlechtem Wirkungsgrad. Ideal bis 80 bar. Bei hohen Drücken wird eine große Antriebsleistung benötigt. | 50–85 % | 150 bar | 60–80 μm |
Plungerpumpe | Kolbenpumpenprinzip für sehr hohe Drücke. Allerdings schlechter Wirkungsgrad. Benötigt sehr hohe Antriebsleistung und sehr gute Filtration. | 60–85 % | 1200 bar | 10–20 µm |
*Empfehlung von Müller Hydraulik basierend auf langjährigen Erfahrungswerten
Die Effizienzklasse einer Pumpe spielt eine enorm wichtige Rolle, wenn es um die Konfiguration einer leistungsopitmalen Kühlschmnierstoff- oder Hochdruckanlage geht. Sie besagt nämlich, im Grunde genommen, wie hoch die motorische Antriebsleistung sein muss, um einen bestimmten Druck bei einer bestimmten Förderleistung erreichen zu können. Dabei gilt es immer auch, die Leistungskurve einer Pumpe in Zusammenhang mit ihrem Motor zu beachten. Hier gibt es große Unterschiede. Leistungsoptimale Pumpen haben in der Regel einen stabilen Druck-Leistungs-Verlauf. Weniger Leistungsoptimale Pumpen hingegen fallen sehr oft in der Leistungskurve ab. Das kann zu Problemen in der Prozessstabilität während der Leistungserstellung führen.
Immer wieder wird auch die Flügelzellenpumpe als Hochdruckpumpe ins Feld geführt. Diese Pumpe ist eine technisch sehr wertvolle, auch sehr effiziente Pumpe, jedoch ausgestattet mit einem sehr filigranen Innenleben, welches nach unseren Erfahrungswerten, je nach Medium und Filtration, schnell zum Verschleiß neigt. Daher setzten wir diese Pumpentechnologie bei der Herstellung von Kühlschmierstoffanlagen für Werkzeugmaschinen nicht ein.
Relevante Pumpentechnologien
Nachstehend erhalten Sie einige Detailinformationen zu den vier von uns heute eingesetzten Pumpentechnologien. Wir bieten Ihnen zur Hochdruckerzeugung auf unseren Hochdruckanlagen und Druckerhöhungsanlagen und Hochdruck-Förderer-Kombinationsanlagen folgende Hochdruckpumpen-Technologien als Kernkompetenzen:
Kolbenpumpe (Axial- oder Radial)
- Ausführung als mechanische Regelpumpe mit höchster Energieeffizienz (eco+ Regelpumpe)
- Ausführung als Konstantpumpe ohne mechanischen Regler aber dafür mit Frequenzumrichter (eco+ Frequenzumrichter)
Zahnradpumpe
- Konventionelle Zahnradpumpe im robusten Gussgehäuse und mit gehärteten Zahnrädern ohne und mit eco+ Frequenzumrichter
- Innenzahnradpumpe ohne und mit eco+ Frequenzumrichter
Schraubenspindelpumpe ohne und mit eco+ Frequenzumrichter
Plungerpumpe ohne und mit eco+ Frequenzumrichter
Warum KSS-Hochdruck? Wann welche Hochdruck-Pumpentechnologie?
Hochdruckanlagen in der Zerspanung mit Werkzeugmaschinen mit Drücken deutlich über 50 bar kommen heute in erster Linie zur allgemeinen Unterstützung des Zerspanungsprozesses zum Einsatz. Dabei gibt es viele positive Aspekte zu beobachten, die wir an anderer Stelle besser ausgeprägt dargestellt haben (ggf. Link zu Vorteile Hochdruckzerspanung). Aber egal bei welcher Anwendung und in welchem Kühlschmierstoffmedium, fast immer beobachtet man die enorme Verbesserung der Standzeiten bei den eingesetzten Werkzeugen, sowie bei der Oberflächengüte der Werkstücke. Diese Vorteile kann man im Grunde genommen bei jeder Zerspanungsart, wie auch auf verschiedensten Werkzeugmaschinentypen feststellen, sei es eine konventionelle Drehmaschine, eine mehrspindlige Werkzeugmaschine oder gar ein Bearbeitungszentrum. Als Hersteller haben wir hier ein breites Angebot in Form eines Baukastens für alle Anwender mit Ausnahme von Schleifmaschinen, die wir momentan noch nicht bedienen.
Im speziellen jedoch gibt es hier einen Werkzeugmschinentypen, auf welchen wir uns ganz besonders konzentrieren: die Langdrehautomaten. Hier sind wir mit unseren vielfältigen Lösungsansätzen rund um die im Markt erhältlichen Maschinentypen, Marktführer in Europa.
Was ist ein Langdrehautomat?
Ein Langdrehautomat ist eine spezielle Werkzeugmaschine, die in der Fertigungstechnik eingesetzt wird, um präzise und komplexe Drehteile aus verschiedenen Materialien herzustellen. Diese Maschinen sind besonders für die Serienproduktion von langen, zylindrischen Bauteilen geeignet, da sie eine hohe Automatisierung und Effizienz bieten. Langdrehautomaten können mehrere Bearbeitungsschritte in einem Durchgang durchführen, was die Produktionszeit verkürzt und die Genauigkeit erhöht. Zerspant wird mehrheitlich unter Verwendung von Schneidölen zur Werkzeugkühlung. Insbesondere zeichnet sich er Zerspanungsprozess durch die Bearbeitung von hochlegierten Werkstoffen aus, in denen häufig sehr kleine und tiefe Bohrungen vorzunehmen sind. Aus diesem Grund wird der Langdrehautomat sehr häufig mit sogenannten Hochdruckanlagen für innengekühlte Werkzeuge ab Werk ausgerüstet oder aber im Feld nachgerüstet. Sie sind häufig in der Automobilindustrie, im Maschinenbau und in anderen Bereichen der industriellen Fertigung zu finden. Im Speziellen in der Medizintechnik, Uhrenindustrie, Motoren- und Getriebteilefertigung, sowie in Teilen der Möbelindustrie u.v.m.
Was macht uns mit unseren combiloop, combistream und chipstream-Anlagen so attraktiv für die Welt der Langdrehautomaten?
Betreiber von Betriebsstätten mit Langdrehautomaten sind in der Regel auf hohen Output ausgelegt. Sie benötigen schnelle Zykluszeiten, sehr hohe Drücke, hohe Präzision bei optimaler Raumnutzung, sowie maximaler Energieeffizienz. Und hier kommen wir ins Spiel: egal ob eine Platzierung der Hochdruckanlage unter dem Stangenlademagazin oder parallel dazu, wir haben die Baukastenlösung bei Drücken bis zu 300 bar und Förderleistungen von bis 60 l/min. Und das im Standard. Aber dies toppen wir noch mit einem einzigartigen Energieeffizienz-Konzept, welches sich vor allen Dingen bei Anwendungen im Schneidöl auszeichnet und seine ganze Klasse bei hochlegierten Werkstoffen, sowie bei filigranen und tiefen Bohrungen zeigt. Unter Einsatz unserer eco+ mechanisch selbstregelnden Kolbenpumpe erzielen wir spitzen Energieeinsparmöglichkeiten im Vergleich zu anderen Technologien für unsere Partner und Kunden. Dies möchten wir am nachfolgenden Beispiel wirtschaftlich aufzeigen:
Mehrwert Regelpumpe versus Frequenzumrichter
- Regelpumpe hat 100-prozentigen Regelbereich (bis zu 0 l/min zu fördern)
- Frequenzumrichter haben einen maximalen Regelbereich von 70%. Bei 20 l/min maximaler Pumpenleistung werden immer mindestens 6 l/min gefördert).
- Keine Verlustenergie bei mechanischer Regelpumpe gegenüber Frequenzumrichter.
- Keine zusätzliche Kühlung des Schaltschranks notwendig, im Vergleich zu dort verbauten Frequenzumrichtern.
Exemplarische Modellrechnung Einsparungspotenzial RKP / eco+
- Gewünschter Arbeitsdruck: 150 bar
- Maximale Förderleistung: 20 l/min.
Annahme Rahmenbedingungen bei der Herstellung eines Drehteils:
- Zweischichtbetrieb 16 Stunden am Tag
- 230 Jahresarbeitstage
- Zur Herstellung des Drehteils werden 50 % Hochdruckeinsatz pro Zyklus gerechnet
- Es werden 0,24 € durchschnittliche Stromkosten angesetzt
- Regelverlust Frequenzumrichter (FU): 70 %
eco+ Regelpumpe | Zahnradpumpe mit FU | Schraubenspindelpumpe mit FU | Flügelzellenpumpe mit FU | |
---|---|---|---|---|
Leistungsaufnahme in kW | 5,556 | 5,882 | 7,692 | 5,882 |
Gesamtkosten im Jahr in EUR | 2453,33 € | 2597,65 € | 3396,92 € | 2597,65 € |
eco+ Stromkosten im Jahr in EUR | 1796,49 € | 2139,85 € | 2940,94 € | 2139,85 € |
Mögliches Einsparpotential eco+ Effekt | -656,84 € | -457,80 € | -455,99 € | -457,80 € |
Verlustleistung FU in EUR | 0 € | 256,08€ | 351,99 € | 256,08€ |
Zusätzliche Kühlung FU in EUR | 0 € | 128,04 € | 175,99 € | 128,04 € |
Stromkosten effektiv im Jahr in EUR | 1796,49€ | 2523,96 € | 3468,92 € | 2523,96 € |
Mögliches Einsparpotential (in %) Regelpumpentechnologie versus... | 29 % | 48 % | 29 % |
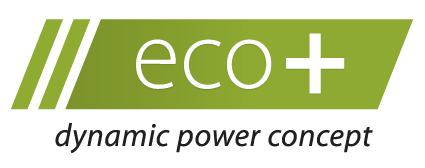
Für Drücke über 80 bar und Fördermengen deutlich über 16 Liter pro Minute kommen bei Müller unter dem Konzept eco+ dynamic power concept entweder geregelte Kolbenpumpen oder frequenzgerichtete Antriebe zum Einsatz. Generelle Vorteile des eco+ dynamic power concept: erhöhte Energieeffizienz, geringerer Wärmeeintrag, erhöhte Temperaturstabilität, höherer Wirkungsgrad. Gerade die eco+ Regelpumpentechnologie steht für geringeren Wärmeeintrag durch perfekte Ressourcennutzung. Die hohe Leistungseffizienz der Pumpe bedingt geringere Antriebsleistungen im Vergleich zu herkömmlichen Konstantpumpen und kombiniert dies mit der mechanischen Anpassung der Förderleistung an den tatsächlichen Bedarf. Die Pumpe zeichnet sich auch durch ihre ruhige Laufleistung aus. Zusätzliche Kundenvorteile: keine störenden Hochfrequenztöne in der Fertigung, geringere Energiekosten!